Roof Inspections
The condition of a roof is a surefire indicator of the condition of the structures below. A roof protects the house from the elements and provides a water-resistant barrier to rain. Every home inspection should include a roof inspection as it is the one component of the house that most potential homeowners don't get to see up close before purchasing their dream home.
Roof coverings and slope
A home inspector begins a roof inspection by looking at the roof covering and its slope. A roof is designed to shed water and the slope of the roof aids in that process. Each roof type has a minimum slope to fulfill this requirement and this will need to be determined. A metal roof due to its nature requires a far lesser slope than that of a tiled roof. An assessment will be made of the condition of the roof covering. In the case of a metal roof any rust will be noted as an item requiring correction whereas with a tiled roof any broken or dislodged tiles will be noted. A home inspector may or may not walk on the roof depending on accessibility, safety and the nature of the roof coverings. It is inadvisable in many cases to walk on a roof as it may cause damage e.g. older IBR roofing or concrete tile. We generally use a drone to assess the condition of a roof and take many photos for our clients. Roofing systems and their components can be quite confusing so we will always include a short explanation of the components and the purpose of their function in the roofing system.
​​
​
​
​
​
​
​
​
​
​
​
​
​
​
​
Assessing a home with a flat (more correctly stated low slope) roof is a lot more challenging as the slope of the roof is minimal and the roofing system is very much dependent on the non-visible waterproofing that an inspector will be unable to see. The roofs are either finished with gravel which protects the roofing from the UV rays or mineral granules, aluminium and elastomeric finishes as pictured below.
​
​
​
​
​
​
​
​
​
​
​
​
Underlayment
​
The need for taking care in the design, the construction and erection of roofs and fixing of the roof covering is essential to ensure water penetration into the interior of the building is avoided. There is an absolute requirement in roof construction to prevent water reaching the interior of a building and where two kinds of rainfall intensity need to be considered:
-
Rain falling vertically
-
Rain driven by wind
Both categories contribute to the total quantities of rainwater needing disposal, but the second category particularly affects the weather tightness of lapped roofing, such as tiles and slates, and even the direction and extent of lap of larger sheets; with many manufacturers recommending the use of underlays, fixing of tiles etc. in these applications.
One must remember that rain falling while the wind is blowing affects pitched roofs more than flat (and walls even more so), it is therefore important to consider one’s geographical location and associated weather patterns.
​
In current building practice, the undertile membrane has become an integral part of any tiled roof. It will provide a highly effective barrier against the ingress of wind-driven rain and dust. The pressures exerted by wind forces will also be substantially reduced due to pressure equalisation, greatly reducing the risk of wind uplift.
​
​
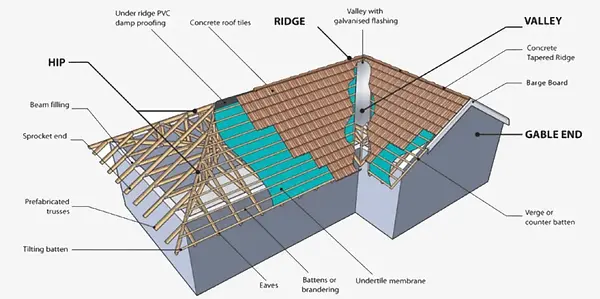
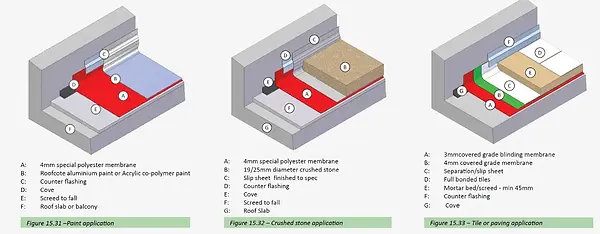
Flashing/Waterproofing
Most roofing issues occur due to failed, poor or absent flashing. Flashing typically is present at all places where a vertical wall meets the roof. But they could be found in other areas. More common types of flashing are :
Sidewall Flashing – Is used in waterproofing the sheet which ends, runs and seals a parapet. Used in conjunction with either a steel or a membrane type counterflashing.
Headwall Flashing – To waterproof the top end of the sheet where it butts with a parapet or headwall. Used in conjunction with either a steel or membrane type counterflashing.
Counter Flashing – In conjunction with head- & sidewall flashing. It is partially recessed into the wall to complete the waterproofing process.
Soaker Flashing – If a roof penetration is close to a ridge capping (or flashing above the penetration), you can fit a simple flat tray on top of the roofing so that it extends from under the capping down to a sleeve around the penetration.
Valley Flashing – Used as a gully between two adjoining roof planes.
​
​
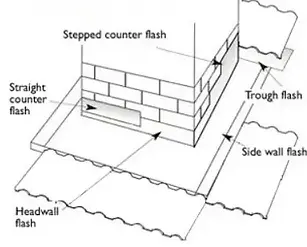

Bitumen and acrylic waterproofing can also be found as well. It is with acrylic waterproofing that most failures are found however as the use more often than not was not for its intended purpose.
​
Chimney flues can also have boots which are very effective at preventing the ingress of water.
​
​
​
If you are interested in this service please check our pricing and contact us today. We are certified roof inspectors and look forward to your call.

